I.Introduction of chlorosulfonated polyethylene Chlorosulfonated polyethylene is a kind of special rubber produced by chlorination and chlorosulfonation of polyethylene. After chlorination and sulfonation of polyethylene, the regularity of its structure is destroyed, and become soft and flexible chlorosulfonated polyethylene rubber at room temperature. Chlorosulfonated polyethylene is obtained by dissolving polyethylene in carbon tetrachloride, tetrachloroethylene or hexachloroacetylene, and treating it with azodiisobutyronitrile as catalyst or under ultraviolet irradiation by passing in a mixture of chlorine and sulfur dioxide or with sulfenyl chloride SO2CI. Chlorosulfonated polyethylene is white or milky white flaky or granular solid, relative density 1.07~1.28. Its solubility parameter δ=8.9, easily soluble in aromatic hydrocarbons and chlorinated hydrocarbons; less soluble in ketone, ester, cyclic ether; insoluble in acid, aliphatic hydrocarbons, mono-alcohols and diols. Chlorosulfonated polyethylene rubber at 121 ° C and above for several hours of continuous heating, sulfenyl chloride based on the cracking will occur, so that the polymer and its soluble viscosity increases, processing is prone to early vulcanization phenomenon. II.The basic characteristics of chlorosulfonated polyethylene The chemical structure of chlorosulfonated polyethylene is completely saturated, the saturation of the structure makes it have many characteristics, due to the molecular chain without the existence of double bonds, the vulcanization mechanism is different from other rubbers. Compared with unsaturated rubber, chlorosulfonated polyethylene vulcanized rubber has the following excellent properties. 1.Excellent ozone resistance The products made from it do not need to add any anti-ozone agent. 2.Heat resistance Chlorosulfonated polyethylene with antioxidant heat-resistant temperature up to 150 ℃ (short time). For the use of products below 120 ℃, it is appropriate to use 2 parts of antioxidant BA (butyraldehyde aniline condensate); for products above 120 ℃, it is appropriate to use 2 parts of antioxidant BA and 1 part of antioxidant NBC (nickel dibutyldithiocarbamate) and use. 3.Chemical resistance Chlorosulfonated polyethylene has good chemical resistance.
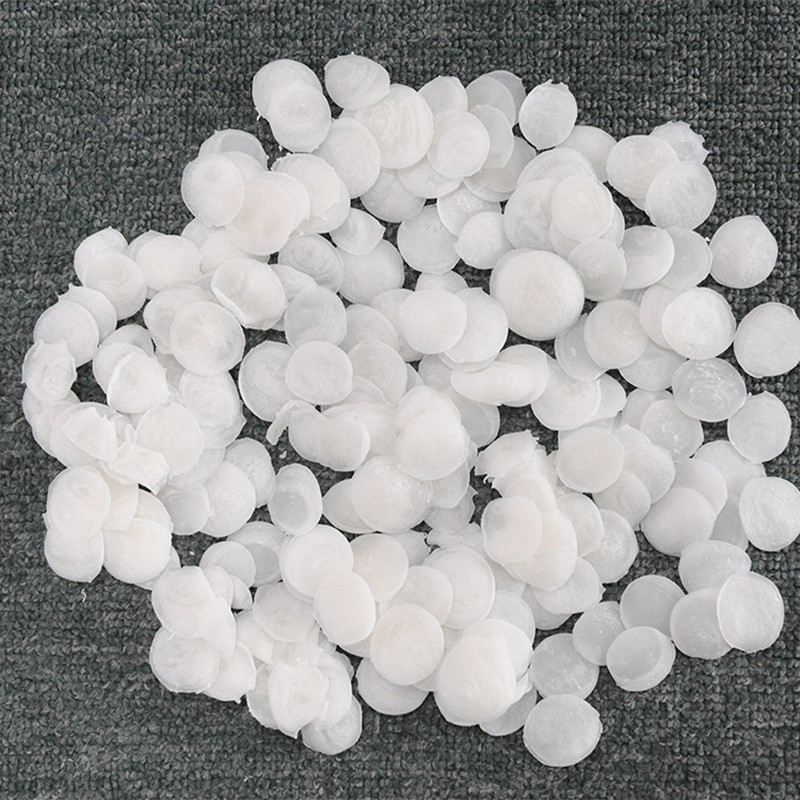
4.Weathering resistance Chlorosulfonated polyethylene has very good weathering resistance, especially when used with appropriate UV masking agents (such as titanium dioxide, carbon black, etc.). Among them, chlorosulfonated polyethylene 40 is the best. 5.Low temperature characteristics Chlorosulfonated polyethylene has good low-temperature resistance, it can maintain a certain degree of flexibility at -40℃, and become brittle at -56℃. 6.Material mechanical properties Chlorosulfonated polyethylene has a strength of more than 20MPa without carbon black reinforcement, and can be used to prepare various light-colored products. In addition, its abrasion resistance is very good, comparable to low-temperature styrene-butadiene rubber. 7.Flame resistance As chlorosulfonated polyethylene contains chlorine atoms in its structure, it will not be flammable, and it is a kind of heat-resistant rubber second only to chloroprene rubber. Chlorosulfonated polyethylene can also be used in conjunction with a variety of rubbers to improve the ozone resistance and weather resistance of the rubber used in conjunction. In addition, chlorosulphonated polyethylene also has its disadvantages: such as compression permanent deformation, low temperature elasticity is poor, oil resistance is not as good as nitrile rubber, the cost is higher than chloroethanol, chlorinated polyethylene and so on.
III.Application of chlorosulfonated polyethylene Chlorosulfonated polyethylene is known for its excellent resistance to ozone and weather aging, as well as its excellent resistance to oil, chemical media and mechanical properties. Therefore, chlorosulfonated polyethylene is widely used in wire and cable coverings, cable insulation, hoses, tapes, automobile parts, building waterproofing equipment, tank linings, rubber sheets, anticorrosive coatings and so on. 1.Building materials One of the main uses of CSM is as industrial pools, tanks, reservoirs lining and single-layer roof waterproof layer. In these applications, CSM is usually used in the form of an unvulcanized adhesive coil that is bonded at the construction site. In terms of single-ply roof waterproofing materials, CSM is comparable to ethylene propylene rubber, PVC, modified bitumen, neoprene, and chlorinated polyethylene.CSM is an excellent roofing material, and is mainly used in factories where resistance to more oils and chemicals is required. 2.Cable Insulation Material CSM is an ideal material for many kinds of wire and cable sheathing. It has better heat resistance than neoprene and has partially replaced neoprene in some wire and cable applications. Insulated with ethylene propylene rubber, CSM protective sheath of the cable can meet the requirements of the IEEE (International Institute of Electronics and Electrical Engineers) standards for nuclear power plants. PVC and CSM co-cured to create weather resistance or high temperature creep performance of the rubber. CSM film and electrolytic iron foil layer can be pressed into electromagnetic shielding film.
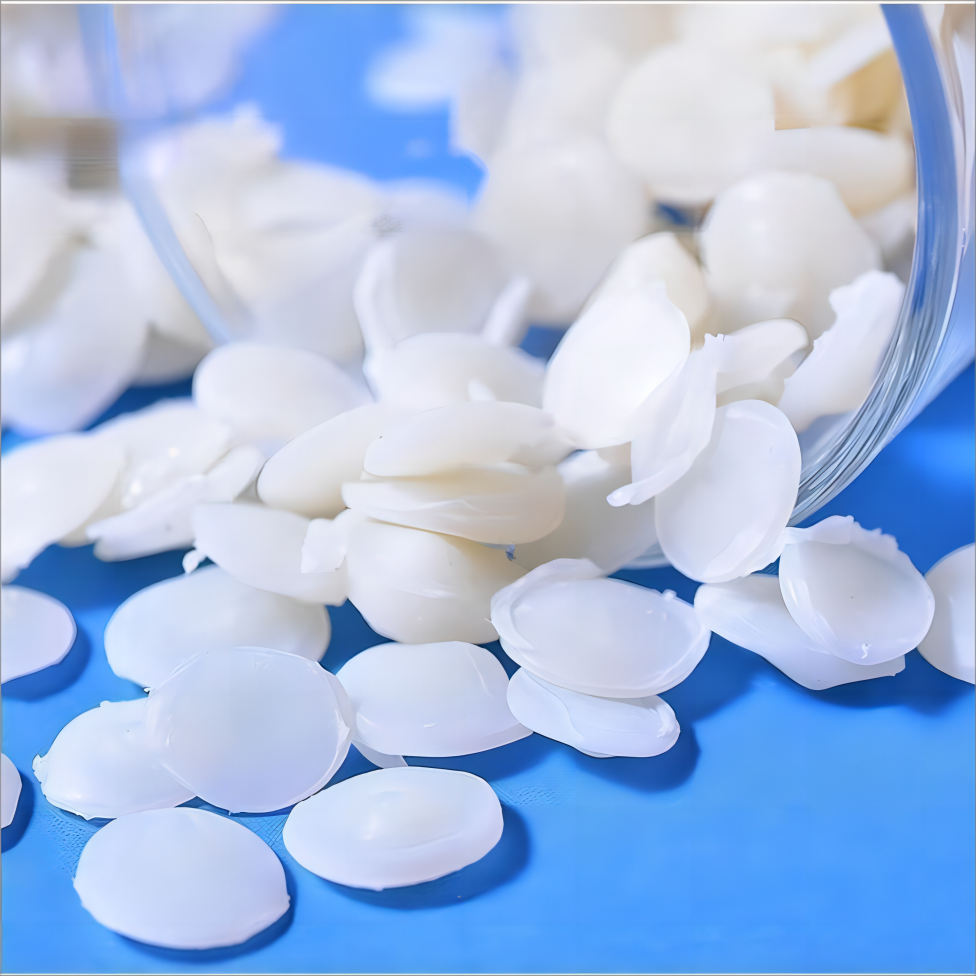
3.Automotive industry CSM is widely used in the automotive industry, mainly used for air conditioning, hydraulic systems, exhaust control, fuel lines and vacuum regulation system device hose. It can also be used as spark plugs and ignition wires, automobile sealing strips, driver's pan primer, etc. 4.Industrial use CSM is used in the industry to manufacture tubes, transportation belts, seals and other products with special properties. For example, the laminated tube made with CSM as the inner layer has low permeability to HFC refrigerant and is suitable for refrigerant transportation tube. Manufacturing CSM - fluorine rubber laminated tube, such as the addition of peroxide, can greatly improve the peel strength of laminated products, the laminated products are suitable for the manufacture of transportation, storage of fuel oil tubes and containers. 5.Paint Coating rubber accounts for about 85% of China's CSM consumption. Using CSM to manufacture the coating film structure saturated, no color genes exist, so the cured coating has excellent resistance to oxidants, ozone, weather aging, ultraviolet, nuclear radiation and excellent resistance to acid, alkali, salt and other properties. The coating is widely used in chemical equipment, steel structures, pipelines, storage tanks, plant buildings, urea ammonium nitrate granulation towers, gas cabinets, sewage tanks, vinyl fire cabinets, trestles, ships and nuclear power plant equipment subject to chemical atmospheric and media corrosion. 6.CSM can be blended and modified with other rubbers. CSM and fluorine rubber blending, can improve the processing performance of blended rubber, CSM and ethylene propylene rubber blending, can improve the physical and mechanical properties of vulcanized rubber and thermophysical characteristics. In the EVA polymer with CSM and isoprene rubber blending can be manufactured slip resistance, abrasion resistance, oil resistance, CSM and PVC, PU in the extruder blending and vulcanization can be manufactured to improve the oil resistance, ozone resistance of the vulcanized rubber.